
Today, prototyping is a crucial part of the industrial product development process to remain competitive in the business. A prototype is a physical representation of a whole product or a component of a product that, although limited in some aspects, can be used for testing, design, and evaluation. Prototypes must be quickly and simply producible, easy and safe to recycle and as an impermanent object of product development, it should be economical.
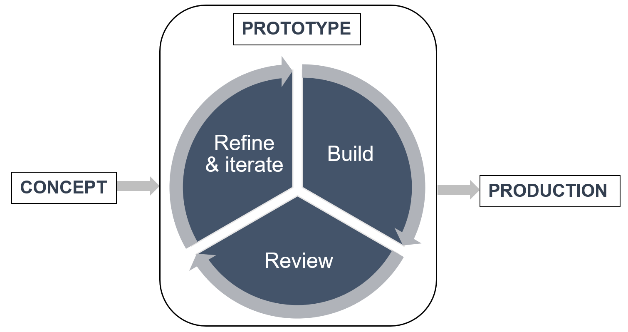
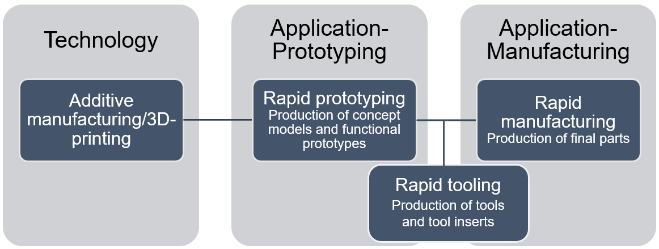
Rapid prototyping, as the name implicates, is referred to different techniques used to quickly and economically produce a model of a product or part of an assembly by using additive manufacturing (Figure 1). Since the 1990’s the term rapid prototyping is associated with additive manufacturing technique. Today rapid prototyping is described as a subset of additive manufacturing that deals with the production of prototypes (Figure 2) (Gebhardt & Hötter, 2016). Additive manufacturing or most commonly named as 3D printing is an additive process of depositing material layer by layer to produce a 3D model of the product or component of an assembly. The traditional manufacturing techniques like injection molding and CNC need expensive tooling and setup, which makes low-volume production of prototypes highly expensive. Rapid prototyping has numerous benefits, but like many other technologies, it too has some disadvantages (Table 1).
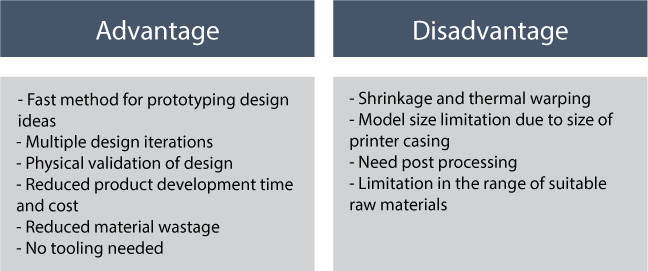
One of the biggest advantages of rapid prototyping over traditional manufacturing methods is that rapid prototyping does not require any special tooling to make the model. For the same reason, the rapid prototyping method is benefited compared to the traditional method in terms of time, energy, money, and material saved (Table 2) (Rathi, 2018). Rapid prototyping has its limitation in the maximum achievable size of the model and lacks the features like creating many moving parts that interlocks and work together like in traditional methods.
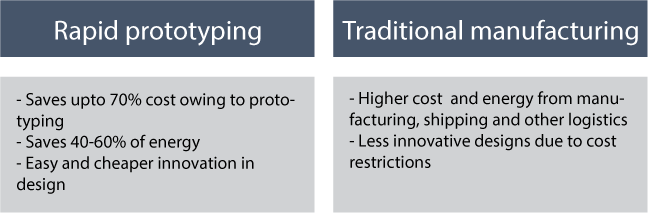
Based on few case studies, Sculpteo, a French rapid prototyping service provider (Sculpteo, 2014), concluded that additive manufacturing compared to injection molding is economically beneficial when considering the production of parts below 500 units (depending on size) and for producing complex objects. Figure 3 represents the data adapted from Sculpteo case study for a car handle (Sculpteo, 2014). This shows that rapid prototyping is economically beneficial over traditional manufacturing when low volume production like prototyping is considered. However, to produce very large prototypes, traditional prototyping methods are economically suitable than rapid prototyping
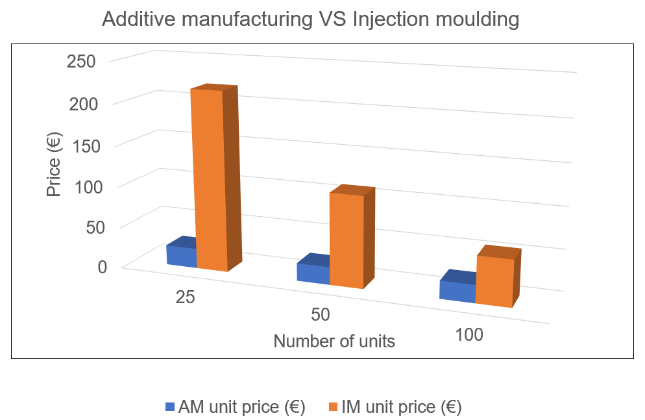
References
Gebhardt, A., & Hötter, J. (2016). 4 – rapid prototyping. In A. Gebhardt, & J. Hötter (Eds.), Additive manufacturing (pp. 291-352) Hanser. Retrieved from http://www.sciencedirect.com/science/article/pii/B9781569905821500058
Rathi, C. (2018, -01-12T08:21:24+00:00). Traditional manufacturing vs 3d printing – A cost analysis. Retrieved from https://precious3d.com/traditional-manufacturing-vs-3d-printing/
Sculpteo. (2014). 3D printing or injection molding: Guide to cost efficiency. Retrieved from https://www.sculpteo.com/en/ebooks/3d-printing-vs-injection-molding/