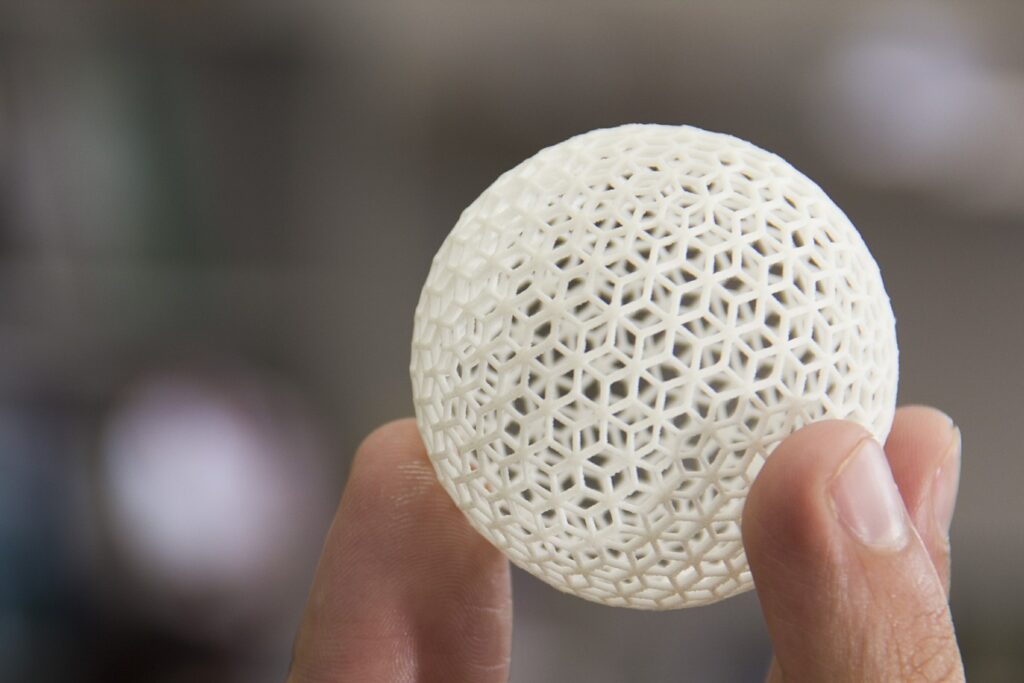
Writers: Rathish Rajan & Simo Huhtanen | Centria | Republished from Centria bulletin
Additive manufacturing (AM) is an emergent technology for manufacturing customized products. It is predicted that a large share of final products will be manufactured by AM methods in the future. The proliferation of AM brings emerging environmental problems such as emissions and waste disposal. Although AM possesses higher material efficiency, material sustainability is an issue that can no longer be ignored due to the wide adoption of AM. This article discusses various choices of bio-based thermoplastic filaments available in the market and those currently in the development stage. Bio-based thermoplastic filaments from renewable sources and biocomposites are an environmentally friendly choice for AM by material extrusion method.
Among the commonly used additive manufacturing methods, fused filament fabrication (FFF) is a material extrusion technology that uses a continuous filament of thermoplastic polymers (Calignano, Manfredi, Ambrosio, Biamino, Lombardi, Atzeni, Salmi, Minetola, Luliano & Fino 2017). The most commercialized thermoplastic filaments are acrylonitrile butadiene styrene (ABS), polylactic acid (PLA), polycarbonate (PC), polyamides (PA) (Ligon, Liska, Stampfl, Gurr & Mülhaupt 2017). The material choice for FFF is currently limited, for example, when compared to conventional plastic processing methods. Moreover, except for PLA, all the thermoplastics mentioned above are produced from non-renewable resources and are non-biodegradable. The FFF method generates a huge amount of plastic waste due to failed prints, support structures, and the produced disposable prototypes (Mikula, Skrzypczak, Izydorczyk, Warchoł, Moustakas, Chojnacka & Witek-Krowiak 2020).
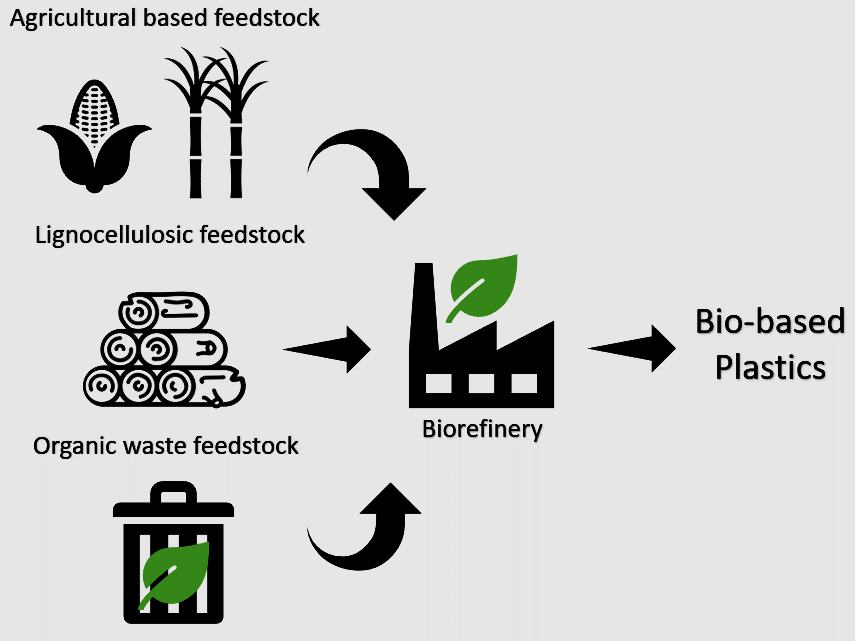
Since additive manufacturing through the FFF method is growing steadily, there is a need to find more sustainable options. Reusing the waste, generated from printing, for making new filaments is a feasible solution. The environmental sustainability of FFF can also be improved by utilizing bio-based plastics (biodegradable and non-biodegradable) for filament making. As explained by European Bioplastics and seen in Figure 1, bio-based plastics are produced from agricultural, lignocellulosic, or organic waste as feedstock (European Bioplastics 2015). As seen from Figure 2, bio-based plastics can be either biodegradable/compostable or non-biodegradable. This article will discuss the commercially available bio-based plastic filaments and explore other promising bio-based polymers suitable for filament production, based on the literature.

Bio-based plastics for FFF
Among the different types of bio-based plastics, the most commonly used filament is those made from PLA. This thermoplastic aliphatic polyester is prepared from renewable sources such as cornstarch or sugarcane. The ratio between the isomers has a vital role in determining the properties of PLA. In the pure form, poly-L-lactic acid or PLLA and poly-D-lactic acid or PDLA are semi-crystalline polymers with a glass transition temperature (Tg) around 57oC and a melting temperature around 175oC. The PLA with a content of 50-90% of L-lactic acid is amorphous in nature. Although amorphous grade has better processability and a wide processing window, the mechanical properties are lower when compared to the semi-crystalline PLA (Farah, Anderson & Langer, 2016). The physical characteristics, such as density, heat capacity, mechanical and rheological properties, are dependent on the Tg of PLA (Farah, Anderson & Langer 2016). The PLA filaments are widely accepted in the FFF method for their ease in printing, low toxic gases produced during printing compared to ABS, lower coefficient of thermal expansion (CTE), and low Tg. However, compared to other FFF plastics such as ABS, PLA has low impact strength, temperature stability, and moisture sensitivity.
Another bio-based plastic considered for additive manufacturing by the FFF method is polyhydroxyalkanoates (PHA’s). PHA’s are aliphatic polyesters derived from microorganisms. PHA’s are synthesized directly via fermentation of a carbon substrate inside a microorganism. Based on the microorganisms and fermentation conditions, homo or co-polyesters with different hydroxy alkanoic acids can be obtained (Basnett, Ravi & Roy, 2017). PHA’s physical and mechanical properties are dependent on the number of carbon atoms in the constituent monomer unit of the polymer chain. The short-chain length PHA’s (five carbon atoms in the monomer unit) are hard, brittle, and crystalline polymers with high melting temperatures, while the medium and long-chain length PHA’s are soft and tough polymer with lower melting point (Basnett, Ravi & Roy 2017). The PHA-based filament is produced by blending with other polymers, especially PLA, and the filaments are commercially available. The reason limiting the use of PHA as a filament in the FFF method is its poor thermal stability, especially the narrow window between the thermal decomposition and the melting temperature. The blends of PLA/PHA have shown improved toughness compared to PLA and PHA alone and is comparable to ABS. The different aspects of the PLA/PHA blend, such as the effect of chain extenders on printability (Fuentes, Thakur, Wu, Misra, Gregori & Mohanty 2020), the influence of plasticizers on the various properties of PLA/PHB filaments, has been recently reported in the literature (Menčík, Přikryl, Stehnová, Melcova, Kontárová, Figalla, Alexy & Bočkaj 2018).
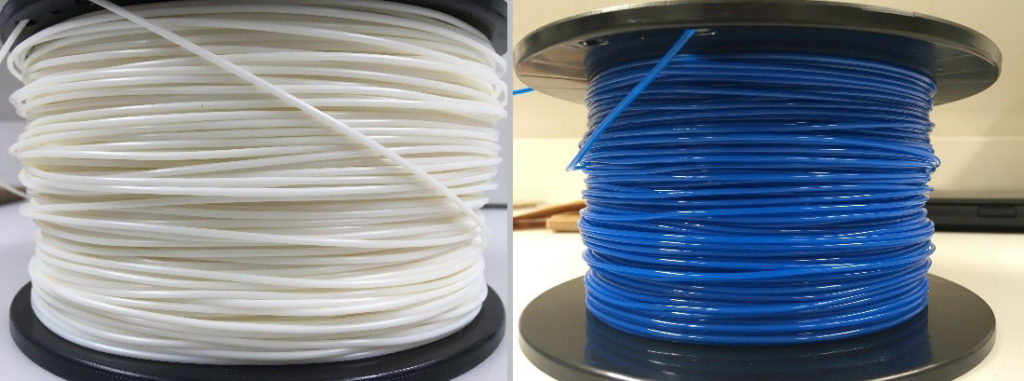
Polybutylene succinate or PBS is a semi-crystalline aliphatic polyester considered for the FFF method and is currently under research due to its excellent ductility and a low melting temperature of less than 120oC. The challenge of using PBS as a filament material is its low melt strength, making it challenging to form continuous monofilament through an extrusion and similarly failing during printing (Ou-Yang, Guo & Xu 2018). Thus, research has been focused on blending PBS with another polymer such as PLA. Researchers have shown that blending of PBS with PLA (above 40 wt.%) resulted in a 3D printed part with high dimensional stability. The PBS/PLA blend filament was highly ductile with elongation of 90-300% when comparing print made from commercially available 3D filaments with typically low elongation at break (Ou-Yang et al. 2018). This study indicates that printing with pure PBS failed due to severe warping and distortion. These results point out the necessity of PBS modification for its application in FFF printing.
The non-biodegradable bio-based plastics such as bio-PE, bio-PP, bio-PET, and a particular type of polyamides are commercially available and contain 20-100% bio-based carbon of total carbon content. Advantages over oil-based variants are reduced carbon emission and decreased dependence on oil while they are chemically similar to the oil-based counterparts. For this reason, these polymers are compatible with currently used recycling methods. Among these plastics, feasibility studies on bio-PE have been done. 3devo printed bio-PE/thermomechanical pulp/MAPE filament successfully (Marco 2018). Diederichs et al. (2019) used bio-based polytrimethylene terephthalate or PTT as a FFF material, and they reported the usage of chain extenders and impact modifiers to improve the printability of PTT. The optimal blend was identified as one with 90 wt.% PTT, 10 wt.% impact modifier, and 0.5 phr chain extender in which the printability and impact strength improved. Although out of the scope of this report, it is worth mentioning that there is FFF filament sold in the brand name of EnviroTM Eco-friendly ABS, which according to 3D Printlife, is biodegradable due to the presence of a bio-additive. Another filament in the same category is bio-based, glycol-modified PET (PETG), containing the additive that triggers biodegradation. PETG has mechanical properties between PLA and ABS. The glycol modification of PET prevents the breaking of filaments, making it an excellent material for FFF printing.
Bio-composites for FFF
Another option to make the product more environmentally friendly is to develop filaments based on bio-based plastics reinforced with natural fiber, which are printable by the FFF method. These reinforcements reduce the consumption of plastics and improve the properties such as strength, stiffness, improves recyclability, reduces warping, make them easier to machine and sand, and give products a natural look.
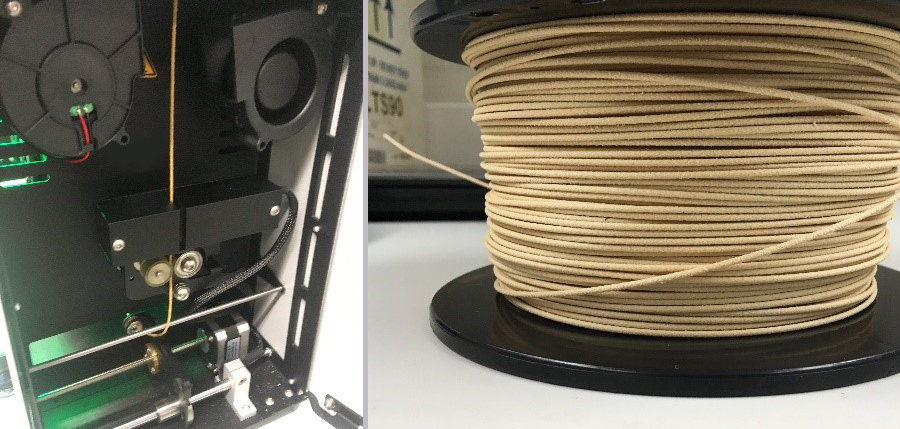
Wood reinforced filaments are already made by Extrudr, Colofabb, Form Futura, and add:north AB. The natural fiber composite filaments sold in the market usually have a PLA matrix. From the category of bio-based non-biodegradable plastics, bio-PE based composites filled with biofibers has been studied. 3D printable filament based on bio-PE/TMP fiber was made at a fibre loading of 10% and 20% (Filgueira, Holmen, Melbø, Moldes, Echtermeyer & Chinga-Carrasco 2018). The non-biodegradable bio-based plastic composites for 3D printing are currently under the research and development stage.
Properties of bio-based plastic
When selecting a thermoplastic polymer to be used as an FFF filament, there are many polymer properties that control the printability and properties of the printed part. The main factors influencing the FFF printing are melting temperature (Tm), glass transition temperature (Tg), and the coefficient of thermal expansion (CTE). The selection of extrusion temperature is based on the melt temperature of the particular polymer. The glass transition and CTE is related to how much thermal stress is formed during printing. The CTE is the tendency of a material to change its shape, area, and volume as the temperature changes. A material with a high CTE value exhibits significant changes in length as a response to temperature change. Thus, a polymer with low CTE will show reduced warping. The chemical resistance, strength, and ductility are other crucial factors influencing the selection of polymer for developing 3D printing filament by the FFF method. Generally, semi-crystalline polymers are less commonly used in FDM because of shrinkage and warpage caused by the formation of crystalline regions during the cooling of deposited layers (Diederichs et al. 2019). Polymers with high crystallinity distort and warp more during FFF printing because of polymer chain condensation when forming crystalline regions, which causes the layers to shrink and pull up from the build platform (Fitzharris, Watanabe, Rosen & Shofner 2018).
Table 1: Thermomechanical properties of bio-based plastics used as 3D printing filaments.
Maker/ research | Brand/ Polymer | Tg (oC) | Tmelting (oC) | Tprinting (oC) | σ max (MPa) | E (GPa) | Ꜫ rupture (%) |
BASF* | Ultrafuse PLA | 61 | 151 | 210-230 | 35 | 2.3 | 4.2 |
Ultimaker* | Tough PLA | 62 | 151 | 205 | 37 | 1.8 | 3.1 |
ColorFabb* | PLA/PHA | > 155 | 195–220 | 61 | 2.9 | 10 | |
Ecker et al. 2019 | PLA80/PHA20 | – | ≈175 | 205 | ≈42 | ≈2.5 | – |
Qing et al. 2018 | PBS60/PLA40 | 51 | 113 | 190 | 46 | 1.5 | 297 |
ColorFabb* | woodfill fine (PLA-PHA/wood fibre) | > 155 | 195 – 220 | 46 | 3.2 | 5.5 |
NB: *Source: respective company websites
According to Chaunier et al. (2018), the bio-based plastics that complies with specifications for material extrusion by the FFF method should be (1) processable above the transition temperature (melt temperature or Tg) and the same should be below the degradation temperature and (2) should have rigidity in the solid-state at room temperature above 1 GPa. The properties of bio-based polymers can be seen in Table 1. According to the above statements, these polymers are rigid at room temperature, have tensile modulus above 1 GPa, and satisfy the material selection specification for material extrusion. The melt flow index MFI is a measure of a material’s flowability and viscosity. The MFI of seven commercial polylactic acid (PLA) grades was investigated as a scale of measuring 3D printing quality (Wang, Capoen, D’hooge & Cardon 2018). A threshold value of 10 g/10 min (2.16 kg; ISO 1133) was recommended for successful printing of PLA at 190–220°C. As most of the commercial bio-based FFF filaments are based on PLA, this value can be used for practical screening of the materials for FFF. In addition to the polymer properties, the success of FFF printing is highly influenced by printing parameters, including bed temperature, nozzle temperature, print speed, and layer height that can affect the properties and printability of the printed part (Diederichs et al. 2019).
The sustainability of materials used for additive manufacturing by material extrusion is of the greatest importance for the future. Bio-based plastic filaments that are made from renewable sources are an eco-friendly choice for 3D printing by the FFF method. PLA is the widely used bio-based plastic in FFF. The filaments based on blends of PLA with PHA and other fillers to improve the toughness of PLA is also available in the market. At the same time, the bio-PE has been demonstrated to be suitable for FFF printing. The viability of using PHA’s and polyethylene furanoate (PEF) as 3D filaments is under research and development. The properties of bio-based plastics discussed in this report satisfy the specifications for 3D printing by the FFF method. The biofiber, when used as reinforcement, has been shown to improve stiffness and reducing warping. When using biodegradable/compostable filaments, it is recommended to select applications requiring low mechanical properties and a shorter life cycle. In the future, the research should be focusing on the recycling of the biodegradable/compostable printing filaments to reuse as new filaments. This enables to adhere to the circular economy framework, which says at least one or two recycling cycles for materials should be ensured as an alternative to the composting or eco-friendly disposal.
Acknowledgments: The research was funded by the EU ERDF, through the INTERREG BSR Programme (ECOLABNET project #R077).
References:
Basnett, P., Ravi, S. & Roy, I. 2017. 8 – Natural bacterial biodegradable medical polymers: Polyhydroxyalkanoates. In X. Zhang (ed.) Science and Principles of Biodegradable and Bioresorbable Medical Polymers. Woodhead Publishing, 257-277.
Calignano, F., Manfredi, D., Ambrosio, E. P., Biamino, S., Lombardi, M., Atzeni, E., Salmi, A., Minetola, P., Iuliano, L. & Fino, P. 2017. Overview on Additive Manufacturing Technologies. Proceedings of the IEEE, vol. 105, no. 4, 593-612.
Chaunier, L., Guessasma, S., Belhabib, S., Della Valle, G., Lourdin, D. & Leroy, E. 2018. Material extrusion of plant biopolymers: Opportunities & challenges for 3D printing. Additive Manufacturing, vol. 21, 220-233.
Diederichs, E. V., Picard, M. C., Chang, B. P., Misra, M., Mielewski, D. F. & Mohanty, A. K. 2019. Strategy To Improve Printability of Renewable Resource-Based Engineering Plastic Tailored for FDM Applications. ACS Omega, vol. 4, no. 23, 20297-20307.
Ecker, J. V., Burzic, I., Haider, A., Hild, S. & Rennhofer, H. 2019. Improving the impact strength of PLA and its blends with PHA in fused layer modelling. Polymer Testing, vol. 78, 105929.
European Bioplastics. 2015. Renewable Feedstock [Homepage of European Bioplastics e.V.], [Online]. Available: https://www.european-bioplastics.org/bioplastics/feedstock/ [2021, Jan 14,].
Farah, S., Anderson, D. G. & Langer, R. 2016. Physical and mechanical properties of PLA, and their functions in widespread applications — A comprehensive review. Advanced Drug Delivery Reviews, vol. 107, 367-392.
Filgueira, D., Holmen, S., Melbø, J. K., Moldes, D., Echtermeyer, A. T. & Chinga-Carrasco, G. 2018. 3D Printable Filaments Made of Biobased Polyethylene Biocomposites. Polymers, vol. 10, no. 3.
Fitzharris, E., Watanabe, N., Rosen, D. & Shofner, M. 2018. Effects of material properties on warpage in fused deposition modeling parts. The International Journal of Advanced Manufacturing Technology, vol. 95, 1-12.
Fuentes, M. A. V., Thakur, S., Wu, F., Misra, M., Gregori, S. & Mohanty, A. K. 2020. Study on the 3D printability of poly(3-hydroxybutyrate- co -3-hydroxyvalerate)/poly(lactic acid) blends with chain extender using fused filament fabrication. Scientific Reports, vol. 10, no. 1, 1-12.
Ligon, S. C., Liska, R., Stampfl, J., Gurr, M. & Mülhaupt, R. 2017. Polymers for 3D Printing and Customized Additive Manufacturing. Chemical Reviews, vol. 117, no. 15, 10212-10290.
Marco. 2018. Bio PE – Extruding the Renewable Polymer – 3devo blog [Homepage of 3devo], [Online]. Available: https://3devo.com/blog/bio-pe-extruding-renewable-polymer/ [2021, Jan 15,].
Menčík, P., Přikryl, R., Stehnová, I., Melcova, V., Kontárová, S., Figalla, S., Alexy, P. & Bočkaj, J. 2018. Effect of Selected Commercial Plasticizers on Mechanical, Thermal, and Morphological Properties of Poly(3-hydroxybutyrate)/Poly(lactic acid)/Plasticizer Biodegradable Blends for Three-Dimensional (3D) Print. Materials, vol. 11, 1893.
Mikula, K., Skrzypczak, D., Izydorczyk, G., Warchoł, J., Moustakas, K., Chojnacka, K. & Witek-Krowiak, A. 2021. 3D printing filament as a second life of waste plastics—a review. Environmental Science and Pollution Research, vol. 28, 12321-12333.
Ou-Yang, Q., Guo, B. & Xu, J. 2018. Preparation and Characterization of Poly(butylene succinate)/Polylactide Blends for Fused Deposition Modeling 3D Printing. ACS Omega, vol. 3, no. 10, 14309-14317.
Wang, S., Capoen, L., D’hooge, D. R. & Cardon, L. 2018. Can the melt flow index be used to predict the success of fused deposition modelling of commercial poly(lactic acid) filaments into 3D printed materials? Plastics, Rubber and Composites, vol. 47, no. 1, 9-16.
Rathish Rajan
RDI Specialist
Centria University of Applied Sciences
Tel. +358 40 594 2702
Simo Huhtanen
RDI Developer
Centria University of Applied Sciences
Tel. +358 40 482 4081